The Internet of Things (IoT) operates as a network enabling sensors, devices, and machines to collect and exchange data through internet connectivity. Diverse industries such as healthcare, agriculture, retail, and transportation stand to gain from these advancements. However, IoT in manufacturing holds particular significance and impact. In this article by Nexle Corporation, we will explore the ways in which the Internet of Things is reshaping the manufacturing industry, including its advantages, disadvantages, and trending use cases.
Top 8 IoT Use Cases and Applications in Manufacturing
1. Remote Monitoring Of Manufacturing Operations
The Internet of Things (IoT) operates as a network enabling sensors, devices, and machines to collect and exchange data through internet connectivity. Diverse industries such as healthcare, agriculture, retail, and transportation stand to gain from these advancements. However, IoT in manufacturing holds particular significance and impact. In this article by Nexle Corporation, we will explore the ways in which the Internet of Things is reshaping the manufacturing industry, including its advantages, disadvantages, and trending use cases.
Business owners and managers can greatly benefit from connecting their industrial assets to the IoT. This allows them to remotely monitor equipment usage and health using IoT sensors. If any issues arise, these sensors can also assist in implementing necessary repairs or maintenance. This approach paves the way for a new business model called “Equipment as a Service.”
Production line energy expenses were cut by almost 40% thanks to the Internet of Things monitoring system. As a result, Armal has reached the end of its digital journey by implementing an IoT solution for manufacturing for real-time power monitoring of all machines.
One such company that employs molding machinery to produce plastic frames and components is Armal, a market leader in the portable toilets industry. They aimed to monitor and improve equipment’s power efficiency.
They could monitor power use in real-time IoT in manufacturing by installing IoT sensors and industrial IoT software.
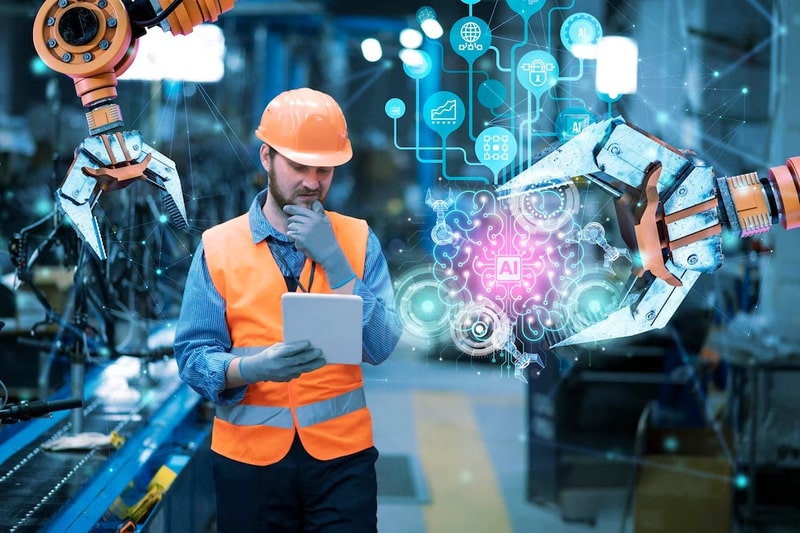
IoT technology for remote monitoring of manufacturing operations
Read more: IoT in Supply Chain and Logistics: Use Cases and Benefits
2. Quality Control
With the help of IoT devices for manufacturing, processes may be tracked and equipment settings updated from afar. As a first step, workers may remotely monitor manufacturing operations and validate that their outputs correspond to regulations. Second, remote tuning and configuration let them save time and effort.
In addition, automated devices are incredibly useful for monitoring and controlling equipment. They streamline the process and allow workers to resolve performance problems remotely through virtual networks. When assets, including mobile ones, are tracked virtually, workers always know exactly where everything is.
3. Predictive Maintenance
Without human supervision, embedded IoT sensors in machines can detect any operational malfunction (regarding temperature, turning number, pressure, voltage, etc.) and alert responsible personnel about equipment deterioration, leaving workers with only the task of repairing it.
Predictive maintenance, or predictive repairing, is a strategy for extending machinery life and lowering operational expenses by identifying potential problems in advance.
To further anticipate when technical support assistance is required, predictive maintenance also enables the integration of Internet of Things – connected devices with sophisticated analytics software.
4. Connected Supply Chain
Using IoT in manufacturing, multiple machinery parts may be networked together to boost the efficiency of the production department as a whole. By collecting real-time data from assets across multiple factories, this IoT network allows the production department to quickly identify and address any issues.
In the operations department, the IoT is useful since it helps save expenses by instantly reporting any problems with connected equipment. This reduces the requirement for more staff that is normally needed to keep an eye on the machinery.
Raytheon manufactures automated systems for collecting data from manufacturing processes. At the Huntsville missile complicated, an Internet of Things device in manufacturing is now analyzing the number of times each screw is turned. If the screw only turns 12 times, the machine will cease operating since it is connected to the Internet of Things and needs to turn 13 times.
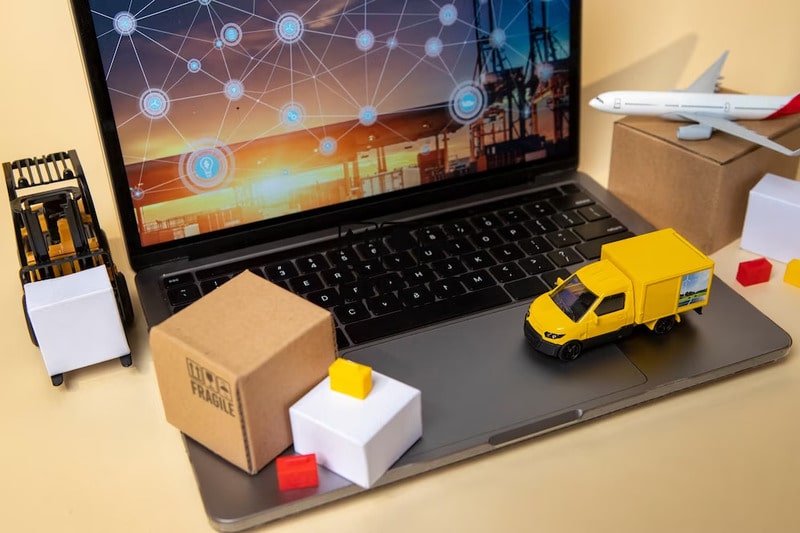
Using IoT in manufacturing results in a connected supply chain ecosystem
5. Robotics Automation
While humanoid robots with human-like knowledge and ability may take some time off, the experience required to develop robotization is incredible. The use of advanced mechanics has become commonplace for tedious, high-precision tasks across a variety of production lines. Many benefits could come from using robots for advanced physics:
- Maintain a pace of constant production with few breaks
- Lessen the possibility of accidents on the job caused by hazardous tasks
- Improved skill and productivity thanks to prompt, unprompted leadership
Mechanical advancements have improved, so they no longer need a human manager. They can independently investigate, arrange, and do a growing list of tasks.
6. Supply Chain Management And Optimization
Internet of Things devices in manufacturing keeps track of stocks and activities in real time. With up-to-the-minute data on available resources, manufacturers can keep checks on their supply chain. Work-in-progress details, equipment collection, and raw material delivery schedule are all provided.
When their IoT solutions for manufacturing are integrated with manufacturers’ up-to-date ERP systems, businesses no longer have to rely on paper records of their operations. As a result, the costs associated with mismanagement and a lack of analysis inside the organization are reduced, and the capability of cross-channel data about several departments becomes available to the stakeholders.
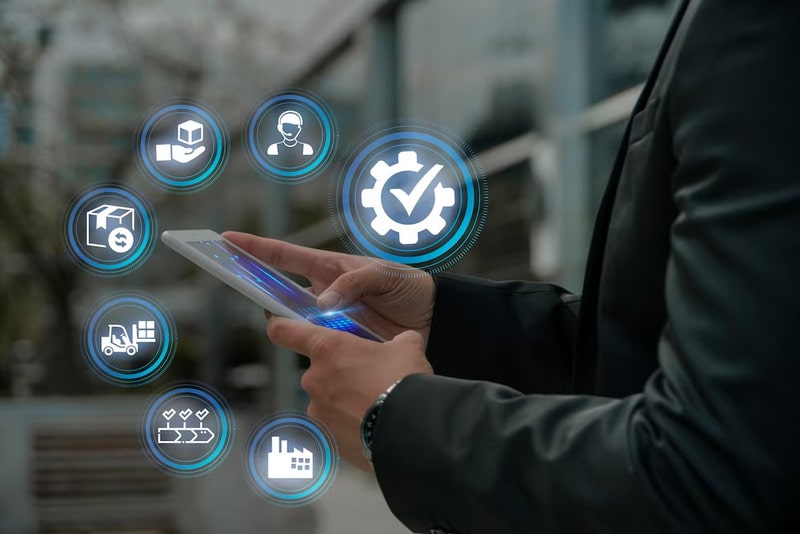
IoT in manufacturing may assist with supply chain management and optimization
7. Digital Twins
Digital twins are virtual replicas of real-world objects, concepts, or areas. They serve as a valuable application of the Internet of Things. These replicas can even include a detailed 3D representation of buildings, encompassing fixtures, machinery, and structure.
Manufacturers can use simulations to test potential changes before implementing them physically. This allows them to assess the impact of these changes beforehand.
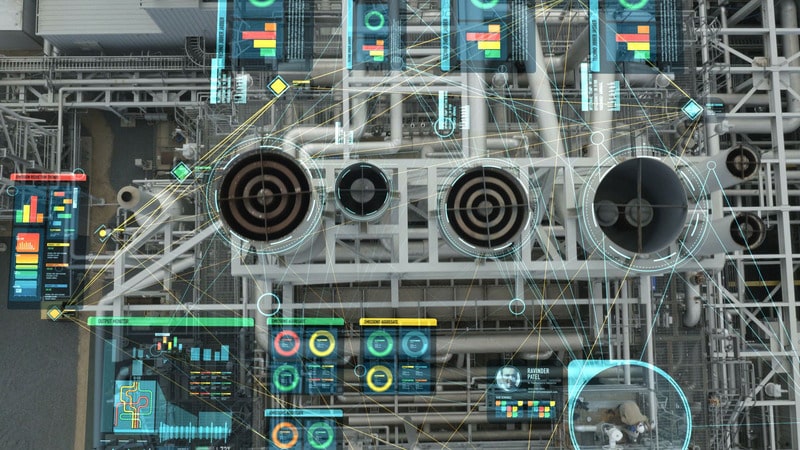
Digital twins – IoT applications in manufacturing
8. Asset Monitoring
It is necessary for businesses to maintain accurate and timely records of their stock and other assets. Thanks to IoT-enabled tracking, monitoring facilities have become easier. This innovation enables remote asset tracking, reducing risk factors, and boosting revenue growth.
This system uses IoT technology to monitor and track assets remotely. It utilizes sensors and devices with GPS or GNSS, which can be installed on a variety of items such as vehicles, kitchen appliances, and factory machinery. With this system, asset management becomes convenient and efficient.
By analyzing sensor data, your machine’s performance can be improved. Connecting your electrical equipment to the Internet of Things also helps them last longer. IoT sensors actively monitoring the environment may provide consumers with an immediate notification in an emergency. Furthermore, this process simplifies the management of past records.
The SumatoSoft Company was hired to develop software for the client’s Big Data and ML solutions. Their main objective was to improve the customer experience when buying refrigerators and to monitor any issues. With Sumatosoft’s software, clients can control their fridges in real-time and receive notifications if anything goes wrong. Moreover, they will also have access to past repair data to ensure problems are addressed promptly.
Read more: What is IoT Device Management: Definition, Benefits, Use Cases
Benefits of IoT in Manufacturing
Cost Reduction
Energy, materials, and downtime losses are the three main factors that manufacturers deal with. Manufacturers may save money while creating new income streams with the use of the Internet of Things thanks to the listed below:
- Optimize asset and inventory management.
- Reduce machine downtime.
- Increase energy efficiency and agility.
- Predictive maintenance and asset and inventory management help companies stop unexpected problems and costs.
Shorter Time to Market
The time it takes to complete a product cycle decreases as manufacturing becomes increasingly quick and efficient. Take, for instance, the vehicle manufacturer Harley-Davidson. With the use of IoT in manufacturing, the company was able to rearrange its York and upgrade its production facility, cutting the time it took to make a single bike from 21 to only 6 hours.
Employee Safety
National Safety Council (NSC) estimates the overall cost of accidental injuries at work in 2019 to be $171.0 billion. Wage and productivity losses and medical and administrative expenses have been calculated into the total. There are also hidden costs, such as the worth of the time of employees who got involved in the accident but did not get a severe injury.
When compared to other industries, manufacturing has a comparatively higher rate of fatalities and injuries per year. Using the Internet of Things in manufacturing to boost factory safety and reduce accidents is set to remain a popular trend.
With sensors, reliable information on the condition of a building or piece of machinery may be gathered. Potential dangers and risks may also be quickly identified. The following are some examples of how IoT solutions for the manufacturing industry might be used to enhance safety measures:
- Wearable devices that monitor technicians’ heart rates and blood pressure. Notifications may be set up to alert users when they are in a potentially dangerous situation while at work.
- Smart sensors may send warnings when temperatures, air pollution, radiation, or sound levels are exceeded.
- Alarms that detect rising temperatures caused by fires.
- Implement preventive maintenance to decommission or repair unsafe machinery before it can cause an accident or damage.
Security and Privacy
Awareness and the security process are essential, and this mindset must spread to every company level. There has been an evolution in recent years toward privacy and security being the top priorities of IT experts. IoT owners worry that the system is at risk of attacks from hackers due to the industrial sector’s popularity.
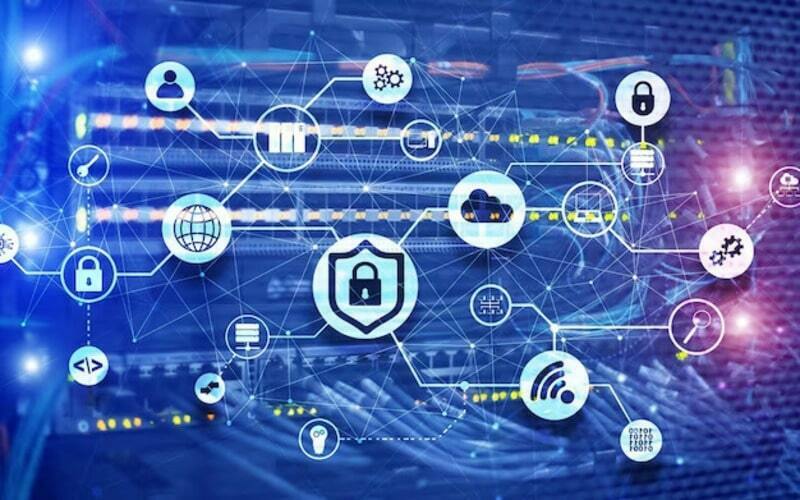
Keep your business secure with IoT
Smart and secure factories are becoming more necessary as the need for safeguarding against hacking of data and virus (or ransomware) infestations grows. Every part of the Internet of Things needs authentication, from the cloud to the network to the programs running on our computers. Some methods to safeguard the IoT ecosystem are:
- Keeping track of real-life IoT devices in manufacturing and preventing them from getting lost or stolen.
- Finding risks along with conducting risk analyses.
- Making use of encryption.
Machine-to-Machine (M2M) Automation
M2M was first used in manufacturing and industrial settings, where SCADA and remote monitoring were already used to manage and remotely control data from equipment. The main function of M2M technology is to gather data from sensors and send it via a network.
One of the most important aspects to consider is the ability of devices to communicate with each other. Smart sensors can be integrated into products to enable this communication. IoT systems can exchange data and autonomously make decisions regarding supply chain management, sales forecasting, and inventory restocking by utilizing sensors.
Manufacturers who are interested in utilizing M2M automation should integrate the data collected into their company applications. By connecting products and machinery through ERP systems, technicians can monitor production efficiency and gain real-time insights. Here are a few instances where M2M has proved to be beneficial:
- Remote monitoring
- Product restocking
- Asset tracking and monitoring
IoT Blended with VR and AR Bringing Digital and Physical Worlds Closer
The benefits of combining VR/AR with IoT data are enhanced. Profit increases, cost savings, new avenues for current product and service lines, and other monetary benefits result.
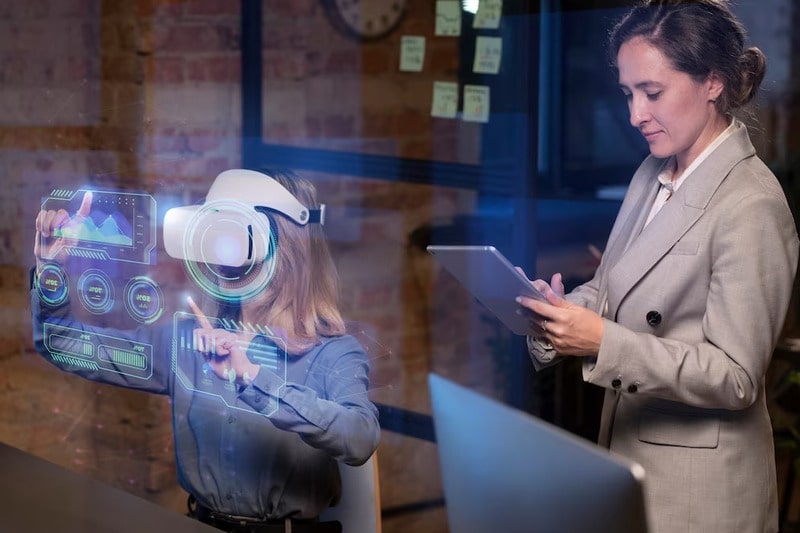
Combining VRAR with IoT devices in manufacturing
In 2023 and beyond, the Internet of Things will be an important development to monitor. Some applications that combine AR/VR with the Internet of Things are listed below:
- Managing equipment
The information gathered by the Internet of Things sensors on equipment conditions may be put as virtual elements to aid in visualizing errors and crashes in real-time.
- Managing spaces
Using AR, factories may better organize stock and design routes that keep employees safe.
- Educating employees
Data from the Internet of Things may be used to model real-world machinery or products, facilitating employee training simulations.
Challenges Of IoT Applications in Manufacturing
Employee Qualifications
The industrial Internet of Things technology requires skilled employees to manage it. However, as the number of smart factories increases, the gap in skills between employers and potential workers keeps getting wider. Moreover, many organizations face challenges because they lack upper-level management with expertise in the Internet of Things.
Executives in the industrial sector may face challenges in making informed decisions about their solutions without sufficient knowledge, capabilities, and expertise in the Internet of Things.
In order to solve this problem, it is important for both employees and management to receive proper teaching, training, and education on IoT devices for manufacturing and other key technologies.
Areas in which both staff and management have little or no experience include:
- Analytics
- Big data
- Embedded software development
- Embedded electronics
- Cybersecurity
- Artificial intelligence
Lack Of Qualified System
Prominent industry experts have found that many workers lack awareness of the Internet of Things. Similar polls have indicated that specialized knowledge in embedded data, electronics, Big Data, and Internet of Things security is essential for the system.
Uncertainty In ROIs
Prominent industry experts have found that many workers lack awareness of the Internet of Things. Similar polls have indicated that specialized knowledge in embedded data, electronics, Big Data, and Internet of Things security is essential for the system.
The manufacturing industry can be completely transformed by utilizing IoT. IoT in manufacturing enables data-driven decision-making, process automation, resource efficiency, and product innovation. It also offers advantages in terms of creating value, customer satisfaction, and gaining a competitive edge. The Internet of Things in manufacturing is not just a tool but a long-term strategy to enhance quality and ensure business success.